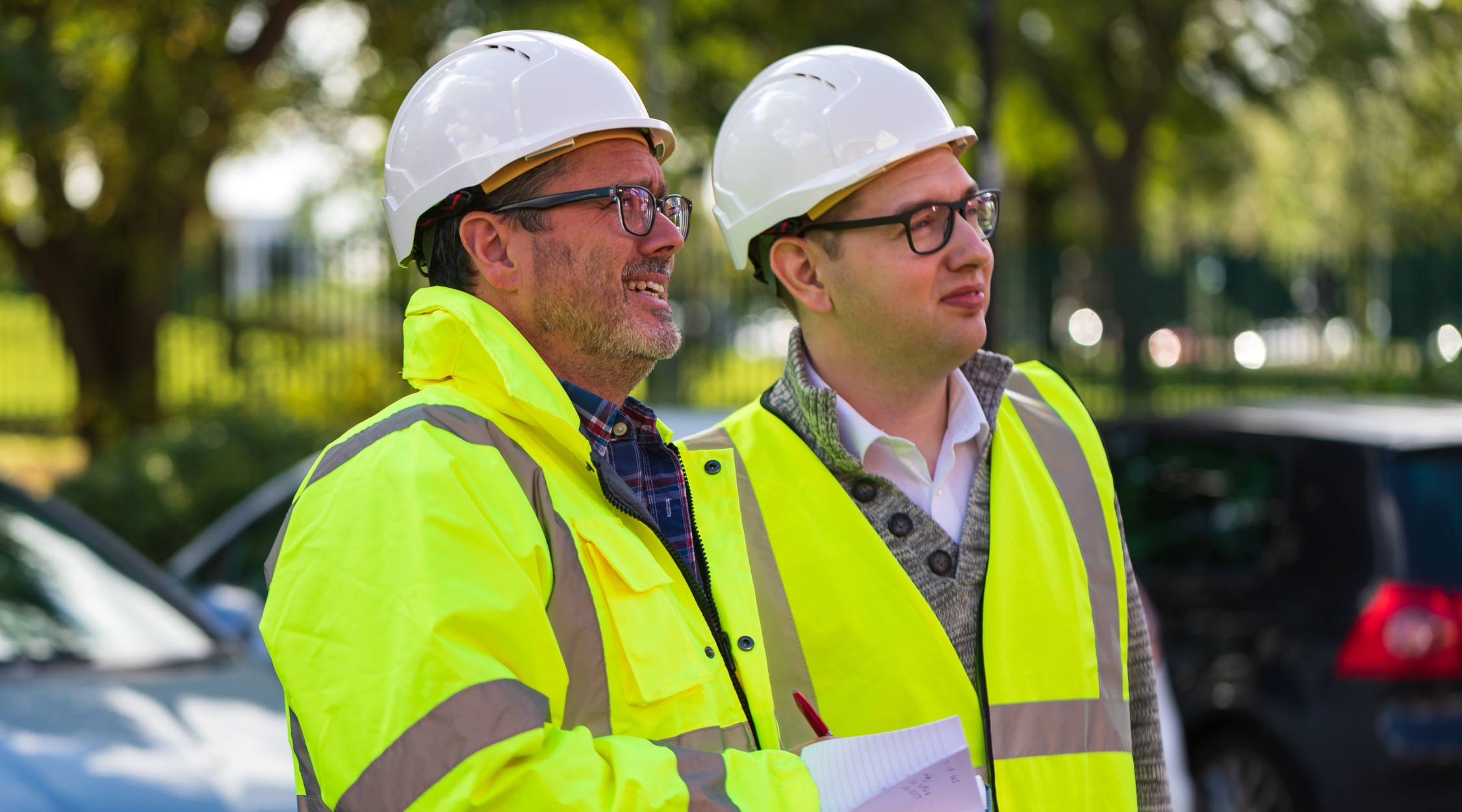
Plan, Do, Check, Act is the model on which the HSE built their guidance (HSG65) for managing health and safety.
The PDCA model is a four-step problem-solving cycle designed to improve business processes. The model, which was developed in the 1920s, focuses on the continuous evaluation of management practices and their willingness to adapt and improve.
The Plan, Do, Check, Act approach achieves a balance between systems and the people implementing them. This means that, regardless of the industry of type of work being completed, the PDCA model can be utilised to achieve management of issues at any level of a business.
By having a constant process of planning, doing, checking and acting, the PDCA framework treats health and safety management as an integral part of good management.
The Four Phases of the PDCA Cycle – Health and Safety:
The PDCA model allows those in health and safety roles to solve problems and implement solutions in a precise, methodical way. Here are each of the four stages in more detail.
Plan:
Consider where you are now and where you need to be, setting the direction for effective health and safety management.
- State what you want to achieve, who will be responsible for what, how your aims will be achieved, and how success will be measured.
- Write down the health and safety policy and your plan to deliver it.
- Remember to plan for any changes and identify any specific legal requirements that apply to you.
Do:
This is the step where the plan is set in motion. The plan was made for a reason, so it is important for employers and employees to carry it out as outlined.
- Profile your organisation’s health and safety risks, identify what could cause harm in the workplace, and what you will do to manage the risk.
- Organise your activities to deliver your plans, aim to involve workers, provide staff training, and communicate with them so that everyone knows their role.
- Decide on the preventive and protective measures needed and put them in place.
- Supervise your staff to make sure that arrangements are followed.
Check:
This is the time to measure your performance and make sure that the implemented plan is working.
- Assess how well the risks are being controlled and if you are achieving your aims, identifying any shortcomings or gaps.
- Investigate any accidents or near misses to establish/identify the root causes.
- Measure performance against your standards in your policies.
Act:
Review your performance and act upon any changes that need to be made.
- This includes learning from accidents and incidents, as well as revisiting plans, policy documents and risk assessments to see if they need updating.
- Take action on lessons learned, including from audit and inspection reports.
- See if the essential principles have been imbedded and are making a difference.
- Report any shortcomings and decide where and how to address any weakness.
Taking each of these steps into action will allow you to manage good health and safety at your workplace and will help your staff feel safe and valued within your organisation.
It is important to remember that PDCA is a loop, not a process which has a beginning and end. The improved process of management becomes the new baseline to which you can further improve.
THSP and the PDCA Framework:
At THSP, we support all four stages of the PDCA model for our customers.
Your health and safety policy is the first step. This is where you identify who does what, where, when and how you are planning the implementation of good practices.
Suitable and sufficient risk and COSHH assessments identify the hazards presented at work, what the risks are and how you intend to eliminate or reduce them to an acceptable level.
Most of our consultants’ time is spent on site with our customers, looking at how work is being carried out. This increased collaboration allows our consultants to offer advice and guidance on how to reduce risk and improve productivity.
The results of these inspections are recorded on each customer’s own Action Management Hub, where they can measure performance, identify trends, and importantly close out any actions identified.
This will help you and your staff establish positive working environments where productivity and safety go hand in hand.
If you need some additional expertise at your workplace and are looking for pragmatic and sensible advice, book a Site Visit with THSP. We will assess your needs and provide the right support.